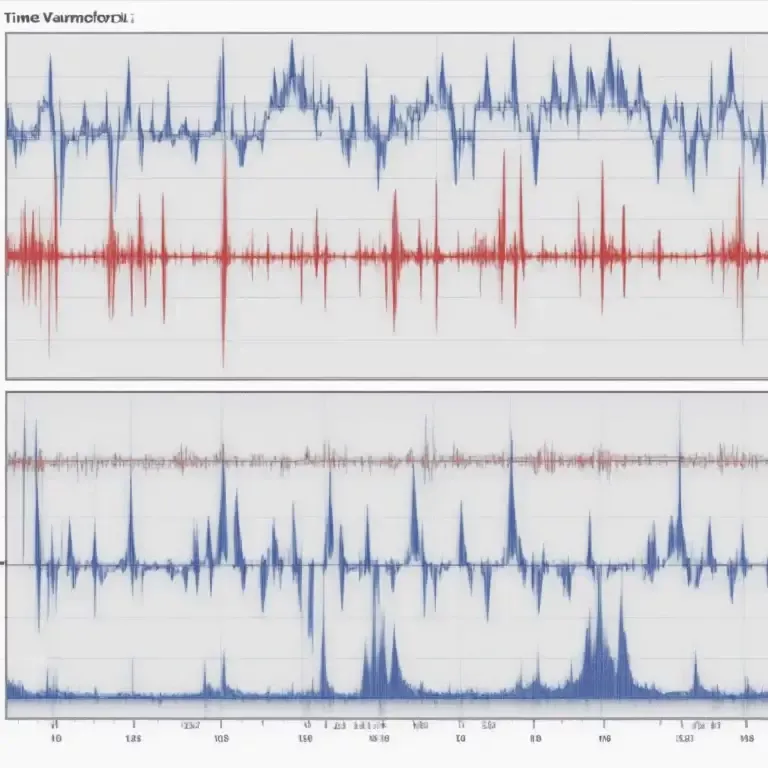
Introduction to reciprocating compressor vibration monitoring
Reciprocating piston compressor
Hey there, reciprocating air compressor enthusiasts! Are you tired of unexpected breakdowns and costly repairs? Well, buckle up because we’re about to dive into the world of vibration analysis for reciprocating piston compressors, including the crucial role of the discharge valve. Trust me, this isn’t your average, snooze-worthy technical talk.
We’re going to explore seven mind-blowing techniques that’ll revolutionize how you maintain your compressors with pressure lubricated or splash lubricated systems, skyrocket efficiency, and save you a ton of cash, especially in positive displacement systems. The compression process will enhance your understanding and strategies for maintenance. Ready to become a vibration analysis wizard? Let’s get shaking!
1. The Basics: What’s All the Buzz About?
First things first, let’s break down why vibration analysis is such a big deal for reciprocating piston compressors. These workhorses are the backbone of many industries, from oil and gas to manufacturing. But here’s the kicker: they’re prone to vibration-related issues that can lead to catastrophic failures if left unchecked. Furthermore, the ability to analyze cylinder pressure versus volume (PV) curves and adherence to API standards is crucial in monitoring these vibrations effectively.
Vibration analysis
Did you know that a whopping 70% of equipment failures in the process industries are due to mechanical issues, with vibration being a major culprit? That’s right, folks – ignoring those telltale shakes and rattles is like playing Russian roulette with your compressor!
2. The Frequency Domain: Your Compressor’s Secret Language
Now, let’s get into the nitty-gritty of vibration analysis. One of the most powerful tools in your arsenal is frequency domain analysis, especially in high-pressure two-stage configurations. Think of it as learning to speak your compressor’s secret language.
By breaking down vibration signals into their frequency components, you can pinpoint specific issues like acceleration effects on:
Unbalance (1x running speed)
Misalignment (2x running speed)
Looseness (multiples of running speed in reciprocating air compressors)
Bearing defects (specific frequencies based on bearing geometry)
Vibration frequency domain
Vibration frequency domain analysis is a crucial aspect of mastering reciprocating compressor vibration monitoring. By analyzing the vibration signals in the frequency domain, engineers can identify the specific frequencies at which the compressor is vibrating. This information can help diagnose potential issues such as unbalanced components, misalignment, or worn bearings. By understanding the vibration frequencies in the frequency domain, maintenance teams can take proactive measures to address any potential problems before they escalate.
Pro tip: Use a waterfall plot to visualize how these frequencies change over time. It’s like watching your compressor’s health story unfold before your eyes!
3. Time Waveform Analysis: Catching the Sneaky Culprits
While frequency domain analysis is great, it’s not the whole story. Enter time waveform analysis – the unsung hero of vibration diagnostics. This technique is particularly useful for reciprocating compressors because it can catch those sneaky, impact-related issues that might slip through the cracks in frequency analysis.
Look out for these telltale signs on your time waveform:
Sharp peaks: Could indicate valve problems or piston slap
Modulation: Might suggest looseness or a cracked component
Truncation: Often a sign of cavitation or liquid slugging in high-pressure compression systems
Time wave form
Remember, combining time waveform and frequency analysis is like having Superman and Batman on your maintenance team – unstoppable with reciprocating air compressor diagnosis!
4. Operational Deflection Shape (ODS) Analysis: See Your Compressor in Action
Ever wished you could see how your compressor moves during operation? Well, with ODS analysis, you can! This technique uses vibration data from multiple points to create a 3D animation of your reciprocating air compressor’s movement.
Operational deflection shape analysis
ODS analysis is a game-changer for positive displacement compressors:
Identifying structural resonances
Pinpointing areas of high stress
Optimizing compressor design and support
Fun fact: ODS analysis has been known to reduce troubleshooting time by up to 50% in complex cases. Talk about a time-saver!
5. Envelope Analysis: Unmasking Hidden Bearing Faults
Bearing problems can be sneaky little devils, often hiding behind louder vibrations from other components. That’s where envelope analysis comes in handy. This technique is like having X-ray vision of your compressor’s bearings.
Envelope analysis works by:
Filtering out low-frequency vibrations in piston air compressors
Amplifying and demodulating high-frequency signals in air compressors
Analyzing the resulting spectrum for bearing fault frequencies
The result? Early detection of bearing issues before they turn into catastrophic failures. It’s like catching a cold before it turns into pneumonia!
6. Cross-phase Analysis: Solving the Mystery of Vibration Transmission
Sometimes, vibration problems aren’t just about a single component – they’re about how vibration travels through your entire compressor system. Cross-phase analysis is your secret weapon for unraveling these complex cases.
By comparing the phase relationship between vibration signals at different points in high-pressure piston air compressors, you can:
Trace the source of vibration in compress air systems
Identify structural resonances
Diagnose coupling and alignment issues
Pro tip: Use cross-phase analysis in conjunction with ODS for a comprehensive understanding of your compressor’s dynamic behavior.
7. Continuous Monitoring: Your 24/7 Vibration Watchdog
Last but certainly not least, let’s talk about continuous monitoring. Gone are the days of periodic frame vibration checks – welcome to the future of real-time analysis for reciprocating piston air compressors that can detect higher frequencies!
Continuous monitoring systems offer:
Early warning of developing issues in air compressors, particularly reciprocating piston air compressors.
Trend analysis for predictive maintenance
Integration with your plant’s control system
Continuous vibration monitoring
Studies have shown that implementing continuous monitoring on reciprocating air compressors can reduce unplanned downtime by up to 70%. That’s like adding an extra day to your production week!
Common Causes of Compressor Vibration
Understanding the common causes of compressor vibration is crucial for effective maintenance and performance optimization. Some prevalent issues include unbalance, which can occur due to uneven mass distribution in the reciprocating components. Misalignment of shafts can also lead to vibrations, particularly in multi-stage systems. Furthermore, looseness in connections or components can create excessive movement. Additionally, bearing issues often present themselves through abnormal vibration patterns, being detectable at specific frequencies depending on the bearing geometry. Recognizing these signs early can prevent severe mechanical failures and costly downtime.
Monitoring Systems and Online Condition Monitoring
Monitoring systems play a vital role in maintaining the health of reciprocating piston compressors and centrifugal compressors. These systems facilitate continuous condition monitoring, allowing for real-time data collection on vibration levels and other critical parameters. Advanced online monitoring technologies, such as the Bently Nevada System 1, provide comprehensive analytics to detect anomalies, malfunctions, and predict potential failures. Utilizing these systems not only enhances operational efficiency but also extends the lifespan of equipment by enabling proactive maintenance strategies. By integrating monitoring systems, operators can ensure their compressors remain in optimal condition, significantly reducing unplanned outages and associated costs.
Checklist for performing basic vibration analysis on reciprocating air compressors:
1. Preparation for all types of reciprocating compressors:
Gather necessary equipment (vibration analyzer, accelerometers, cables)
Review compressor specifications and operating parameters, including psi levels
Ensure the compressor is running at normal operating conditions
2. Safety First (for piston compressor)
Wear appropriate PPE (safety glasses, ear protection, gloves)
Identify and avoid hot surfaces and moving parts
Obtain necessary work permits if required
3. Measurement Setup for reciprocating air compressor work:
Identify key measurement points (bearings, cylinder heads, frame) in hp air compressors
Clean measurement surfaces
Securely mount accelerometers using appropriate methods (magnet, adhesive, stud)
Double-check accelerometer orientation (radial, axial, vertical)
4. Data Collection:
Set up vibration analyzer (input compressor RPM, number of cylinders)
Configure measurement parameters (frequency range, resolution)
Take readings at each measurement point on reciprocating air compressors
Collect both overall vibration levels and spectral data
Repeat measurements to ensure consistency
5. Basic Analysis:
Review overall vibration levels against ISO standards or OEM recommendations
Examine frequency spectra for common fault patterns:
1x running speed (unbalance)
2x running speed (misalignment)
Multiples of running speed (looseness)
Specific bearing frequencies
Piston pass frequency and harmonics
Valve-related frequencies
6. Time Waveform Analysis:
Collect time waveform data
Look for impacts, modulation, or truncation
Compare waveform between cylinders
7. Documentation:
Record all measurement data and observations
Take photos of measurement setup and any visible features
Note any unusual sounds, temperatures, or operational conditions
8. Compare and Trend:
Compare current data with previous measurements
Identify any significant changes or developing trends
Plot key parameters over time to visualize trends
9. Basic Diagnostics:
Identify potential issues based on analysis
Prioritize findings based on severity and criticality
Recommend further analysis if needed (e.g., advanced techniques, oil analysis)
10. Reporting:
Summarize the findings in a clear, concise report
Include raw data, spectra, and time waveforms as appendices
Provide actionable recommendations (e.g., continue monitoring, schedule maintenance)
11. Follow-up:
Schedule next routine vibration check
Plan any recommended corrective actions
Update vibration baseline if significant changes or repairs are made
12. Continuous Improvement:
Review effectiveness of vibration programs for reciprocating air compressors
Identify areas for improvement in data collection or analysis
Stay updated on new vibration analysis techniques and technologies
Remember, this checklist covers basic vibration analysis. For complex issues or critical compressors, consider involving a certified vibration analyst or using more advanced techniques.
FAQs:
How often should I perform vibration analysis on my reciprocating single stage, two stage compressor?
While continuous monitoring is ideal, aim for at least monthly checks if you’re doing periodic analysis. High-criticality compressors might need more frequent attention.
Can vibration analysis detect all types of compressor problems even for pressure lubricated and splash lubricated?
While vibration analysis is incredibly powerful, it’s not a silver bullet. Some issues, like internal leaks, might require additional techniques like ultrasound or performance analysis.
Do I need expensive equipment to perform vibration analysis?
While professional-grade analyzers can be pricey, there are now smartphone-based solutions that can provide basic analysis at a fraction of the cost. Start small and upgrade as needed!
How do I interpret vibration spectra, what should i look for in a multi stage air compressor?
Look for peaks at specific frequencies related to compressor components (e.g., running speed, valve frequencies). Amplitude changes over time can indicate developing issues.
Can vibration analysis predict when my two stage reciprocating compressor will fail?
While it can’t give you an exact date, trend analysis can provide a good estimate of remaining useful life for many components. It’s all about catching problems early!
Why is vibration monitoring important for reciprocating compressors?
Vibration monitoring is crucial for reciprocating compressors as it helps detect potential issues before they escalate, preventing costly breakdowns and downtime. Monitoring vibration levels allows for timely maintenance, ensuring optimal compressor performance and prolonging equipment lifespan.
Vibration Unit Converter
Conclusion:
And there you have it, folks – seven game-changing vibration analysis techniques that’ll transform how you maintain your high pressure reciprocating piston compressors. From speaking your compressor’s secret frequency language to unleashing your inner vibration superhero with ODS analysis, you’re now armed with the knowledge to keep those pistons pumping (piston moves) smoothly.
Remember, vibration analysis isn’t just about avoiding breakdowns – it’s about optimizing performance, extending equipment life, and ultimately saving your company big bucks. So go forth, embrace these techniques, and become the vibration analysis guru your compressors deserve!
Got any cool vibration analysis stories or tips of your own? Drop them in the comments below – let’s keep this conversation shaking (pun intended)!