Embracing the Future: How Industry 4.0 is Revolutionizing the Fourth Industrial Revolution
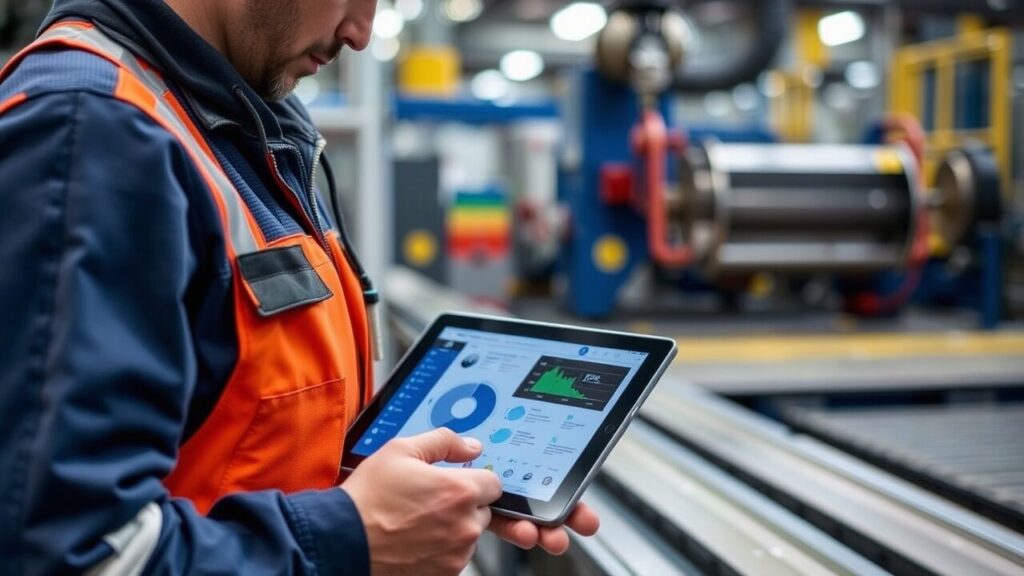
As we stand on the precipice of a technological revolution, Industry 4.0 is transforming the landscape of manufacturing with its digital prowess. This fourth industrial revolution is not just a buzzword; it’s a paradigm shift that promises to automate and optimize every aspect of production. With the integration of advanced technologies like IoT, AI, and big data, factories are becoming smarter, more efficient, and more connected than ever before. Let’s dive into the fascinating world of Industry 4.0 and explore how it’s reshaping the future of manufacturing.
What is Industry 4.0 and How Does it Transform Manufacturing?
Understanding the Fourth Industrial Revolution
The term “Industry 4.0” refers to the fourth industrial revolution, a technological upheaval that is redefining how we perceive manufacturing. Unlike the first industrial revolution, which introduced mechanized production, or the third industrial revolution that brought digital technologies into the mix, Industry 4.0 is all about connectivity and automation. This revolution leverages the power of the industrial internet of things (IIoT), bringing together cyber-physical systems to create a seamless network of machines and sensors. The result is a manufacturing industry that operates with unprecedented efficiency, precision, and flexibility.
The Role of Digital Technologies in Modern Manufacturing
Digital technologies are the backbone of Industry 4.0, acting as the connective tissue that binds various components of the manufacturing process. From AI-driven analytics to real-time monitoring systems, these technologies provide invaluable insights that enhance decision-making and boost productivity. The integration of digital tools allows for the automation of mundane tasks, freeing up human resources to focus on more complex challenges. Moreover, advanced manufacturing techniques, such as augmented reality and robotics, are revolutionizing the production line, making it more adaptive and responsive to market demands.
How Automation Drives Efficiency in Factories
Automation is the secret sauce that transforms ordinary factories into smart factories. By automating repetitive tasks, companies can significantly reduce errors and increase output. With AI and machine learning at the helm, factories can predict maintenance needs and respond proactively to potential disruptions. This predictive maintenance approach not only minimizes downtime but also extends the lifespan of machinery. As a result, the manufacturing operations become more streamlined, and the overall productivity of the factory soars to new heights. Automation, in essence, is the catalyst that propels the manufacturing industry into a new era of efficiency.
How Does the Internet of Things Influence Industrial Operations?
The Impact of IoT on Communication and Connectivity
The internet of things (IoT) is a game-changer for industrial operations, enhancing communication and connectivity like never before. By embedding sensors in machinery and equipment, companies can create a robust network that facilitates seamless data exchange. This connectivity ensures that every component of the production line is in sync, leading to smoother operations and quicker response times. The IoT enables real-time communication between devices, allowing for instant feedback and adjustments. This level of connectivity is crucial for maintaining a competitive edge in the fast-paced world of manufacturing.
Leveraging Real-Time Data for Better Decision Making
In the realm of Industry 4.0, real-time data is the gold standard for decision-making. With advanced analytics tools, manufacturers can leverage this data to gain insights into every aspect of their operations. From monitoring equipment performance to analyzing market trends, real-time data empowers companies to make informed decisions that drive growth and innovation. By harnessing the power of big data, manufacturers can identify patterns and predict future outcomes, ensuring that they stay ahead of the curve. This proactive approach to decision-making is what sets Industry 4.0 apart from its predecessors.
Examples of Industry 4.0 in Action
Industry 4.0 is not just a theoretical concept; it’s a reality that’s already being implemented in factories around the world. For instance, smart factories are utilizing robotics to automate assembly lines, significantly boosting productivity. In another example, companies are using IoT-enabled sensors for predictive maintenance, reducing downtime and optimizing resource allocation. Additionally, AI-driven analytics are being employed to enhance supply chain management, ensuring that products are delivered on time and at the lowest cost. These examples of how Industry 4.0 is being applied demonstrate its potential to revolutionize industrial production and set new standards for efficiency and innovation.
What Technologies Are Central to Industry 4.0?
The Integration of Cyber-Physical Systems
Cyber-physical systems (CPS) are at the heart of Industry 4.0, bridging the gap between the physical and digital worlds. By integrating sensors, software, and network connectivity, CPS enables machines to communicate and collaborate autonomously. This integration allows for real-time monitoring and control of industrial processes, leading to improved efficiency and reduced human intervention. Cyber-physical systems are the foundation upon which smart factories are built, providing the agility and adaptability needed to thrive in a rapidly changing market. As CPS continues to evolve, it will play an increasingly vital role in shaping the future of manufacturing.
Exploring the Potential of Artificial Intelligence in Manufacturing
Artificial intelligence (AI) is a driving force behind the innovation and transformation seen in Industry 4.0. With its ability to process vast amounts of data and learn from patterns, AI is revolutionizing how manufacturers approach problem-solving and decision-making. In the realm of manufacturing, AI can optimize production schedules, enhance quality control, and even predict equipment failures before they occur. This level of intelligence allows companies to operate more efficiently, reduce costs, and improve product quality. As AI technology continues to advance, its potential to reshape the manufacturing landscape is limitless.
The Role of Big Data and Analytics in Industry 4.0
Big data and analytics are the unsung heroes of Industry 4.0, providing the insights needed to drive innovation and growth. By analyzing vast datasets, manufacturers can uncover trends and patterns that inform strategic decisions. From optimizing supply chain operations to enhancing customer experiences, big data analytics plays a crucial role in every aspect of the manufacturing process. The ability to process and interpret large volumes of data in real-time gives companies a competitive edge, allowing them to respond swiftly to market changes and consumer demands. In the world of Industry 4.0, data is indeed king.
How Can Companies Invest in Industry 4.0 Solutions?
Identifying Key New Technologies for Investment
Investing in Industry 4.0 solutions requires a keen understanding of the key technologies driving this transformation. Companies need to identify which technologies align with their strategic goals and offer the most significant potential for return on investment. From IoT and AI to robotics and augmented reality, the array of new technologies available is vast. By focusing on the most impactful innovations, companies can ensure that their investments yield tangible benefits. It’s essential to stay informed about the latest advancements and trends to make informed investment decisions that will propel the business forward.
Strategies for a Successful Digital Transformation
Embarking on a digital transformation journey is no small feat, but with the right strategies, companies can navigate this complex process successfully. A clear vision and well-defined goals are crucial for guiding the transformation efforts. Companies should prioritize building a culture that embraces change and fosters innovation. Collaboration and communication across departments are essential for ensuring that everyone is aligned and working towards the same objectives. Additionally, investing in employee training and development will equip the workforce with the skills needed to thrive in a digital-first environment. With a strategic approach, companies can harness the full potential of Industry 4.0.
Overcoming Challenges in Smart Manufacturing
While the benefits of smart manufacturing are undeniable, companies must also contend with various challenges. One of the primary hurdles is the integration of new technologies into existing systems, which can be both time-consuming and costly. Ensuring data security and privacy is another critical concern, as the increased connectivity of devices presents potential vulnerabilities. Companies must also address the skills gap by investing in workforce training and development. Despite these challenges, the rewards of smart manufacturing are well worth the effort. By proactively addressing these issues, companies can position themselves for success in the Industry 4.0 era.
What is the Future of Manufacturing with Industry 4.0?
Exploring the Shift Towards Industry 5.0
As we embrace the advancements of Industry 4.0, the horizon is already beckoning us towards Industry 5.0. This next phase in the evolution of manufacturing is characterized by a greater emphasis on human-machine collaboration. While Industry 4.0 focused on automation and efficiency, Industry 5.0 seeks to integrate human creativity and innovation into the production process. This shift will lead to more personalized products and services, as well as a renewed focus on sustainability and ethical practices. As we look to the future, the possibilities of Industry 5.0 are both exciting and boundless.
The Evolution of Manufacturing and Supply Chain
The evolution of manufacturing and supply chain processes under Industry 4.0 is nothing short of revolutionary. With advanced technologies at their disposal, companies can optimize every aspect of their operations, from production to distribution. The integration of IoT and AI allows for real-time monitoring and decision-making, ensuring that supply chains are agile and responsive to market demands. This evolution has also led to the rise of smart factories, where automation and data-driven insights drive efficiency and innovation. As manufacturing continues to evolve, the supply chain will play a crucial role in shaping the future of the industry.
How Sustainability is Integrated into Future Manufacturing
Sustainability is becoming an integral part of future manufacturing, with Industry 4.0 paving the way for more eco-friendly practices. Companies are leveraging advanced technologies to reduce waste, conserve energy, and minimize their environmental footprint. From using renewable energy sources to implementing circular economy principles, manufacturers are taking proactive steps towards a more sustainable future. The integration of sustainability into manufacturing not only benefits the planet but also enhances brand reputation and customer loyalty. As we move forward, the commitment to sustainability will be a defining feature of the manufacturing industry.